Here at Johns Manville, we have been manufacturing fiberglass and technical nonwovens for decades. Throughout the years, we have continuously explored their versatile applications, aiming to enhance durability, sustainability, and lightweight product solutions. As a self-sourced company, we operate furnaces producing raw glass, which serves as a base for many of the products we sell. We’ve optimized our production processes over the years, always striving to reduce our environmental impact. Now, let’s take a closer look at JM Engineered Products’ facilities on both sides of the Atlantic Ocean to understand what this means and their sustainability efforts and waste reduction initiatives.
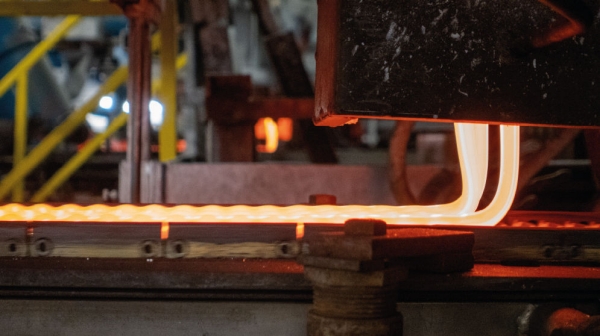
Redefining Waste Recycling in Trnava
Nestled in the picturesque landscape of Slovakia, our Trnava plant stands as JM’s largest site worldwide, boasting over 700 employees. Here, two glass furnaces tirelessly produce glass that is further processed into chopped strands, single-end rovings, and multi-end rovings primarily serving the automotive, transportation, and construction sectors.
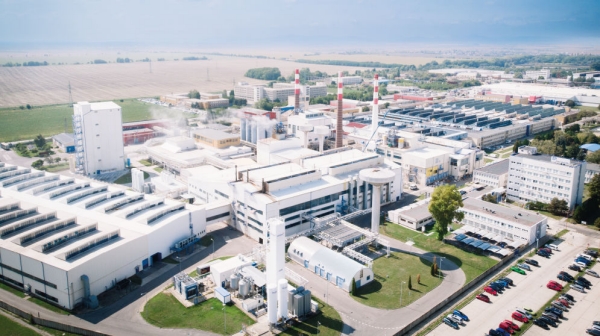
In 2021, we launched a state-of-the-art recycling unit, aligning with the European Commission's zero waste program and our overarching goal of sustainable resource management. This innovative facility boasts a recycling capacity exceeding 3 tons per hour. It comprises a warehousing area, feeding and transportation equipment, a shredder, a burning chamber, and milling machinery. By repurposing glass fiber waste into raw material for on-site production processes, we've effectively closed the production loop, diverting over ten thousand tons of waste from landfills annually. That’s equivalent to one large truck every day.
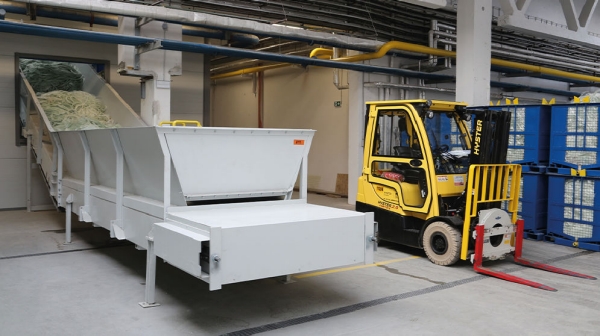
Elena Hríviková, Manager for Environment, Health, and Safety – Europe/Asia, emphasizes our dedication to environmental stewardship: "Our investment in recycling technology underscores our commitment to sustainable practices, ensuring a tangible positive impact on the environment." The plant is ISO 14021:2016 certified (link to certificate), ensuring that all products leaving the plant contain a minimum of 6% recycled content.
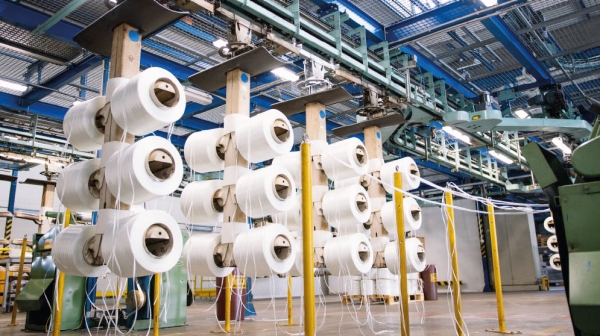
Sustainability Pioneers in Etowah
In the heart of Tennessee, our Etowah plant also operates two glass melting furnaces. These furnaces yield chopped strands and glass fibers which are processed into glass nonwovens. The primary uses for these products are in construction, roofing and specialty applications. Long before sustainability gained the significance it holds today, our teams installed a recycling unit at the plant in 1987. Glass waste that would otherwise end up in landfill gets collected, chopped, ground, and dried, allowing for reintroduction into our furnaces.
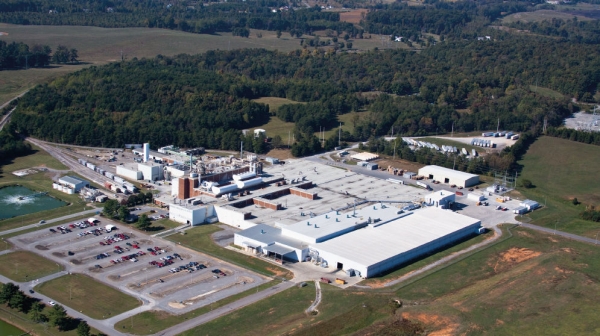
David Kissell, Plant Manager at Etowah, highlights the significance of the unit: "Our process efficiently repurposes furnace scrap, contributing to our sustainability goals. From waste collection to reintroduction into the furnace, our system ensures minimal waste.” This initiative results in a 5% recycled content in our finished products.
Whether we use recycled content or not, customers notice no difference as it has no impact on the product quality. However, it has a significant impact on the environment and reflects our commitment to minimizing waste and maximizing resource efficiency.
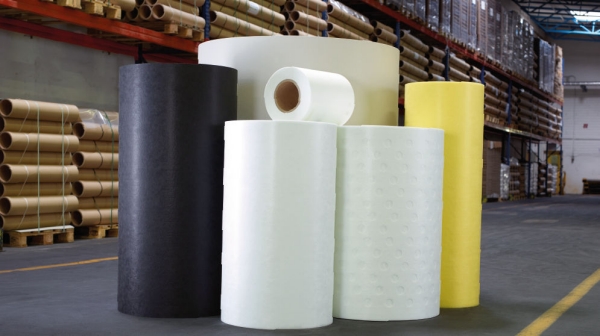
Join Us in Building a Sustainable Future
As we continue to innovate and implement eco-friendly practices, we remain committed to lower our environmental footprint and support our customers in their sustainability journey. Together, let's take practical steps towards a better tomorrow that benefits both the industry and the planet.
Reach out to our team today if you would like to learn more about JM’s sustainability initiatives.
-
Engineered Products
-
Engineered Products
-
Engineered Products
-
Engineered ProductsJohns Manville MultiStar ® 272 - Your Key to Achieving Class A Surface Quality in Automotive Applications
-
Engineered Products